Alternative lifting solutions for heavy loads
14 October 2024
A round up of alternative lifts and news from around the world. Niamh Marriott reports.
Alternative lifting solutions use specialized equipment and techniques to move heavy loads in situations where traditional cranes may not be feasible or efficient. This includes devices like gantry systems, strand jacks, hydraulic skidding systems, and other customised lifting solutions designed for unique challenges, such as limited space, irregular load shapes, or extreme weight.
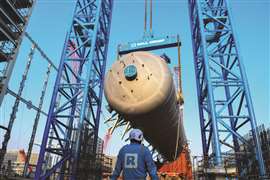
These alternative lifting methods are increasingly important in complex industrial projects, providing innovative ways to safely and effectively manage heavy lifting tasks in diverse environments.
Modular gantry
Heavy lift, transport and installation specialist Roll Group recently made two lifts, each of more than 1,000 tonnes, at a petrochemical plant in Cilegon, Indonesia.
It used its new RMG modular gantry crane equipment for both lifts. The work was part of Roll Group’s combined scope, also using its fleet of self propelled modular transporter (SPMT) and cranes.
To move the C3 lower splitter column prior to uprighting, Roll Group used two sets of 24 axle lines of SPMT, one set under each end of the column. It was 79.6 metres long by 9.36 metres wide and 9.95 metres tall. Weight was 1,042.7 tonnes. The 2400Te gantry system was erected to a total height of 97 metres. As the gantry system uprighted the C3 column it was tailed by a 1,250 tonne capacity Terex Demag CC 6800 crawler crane, a model now designated Tadano CC 68.1250-1.
Implementation of the new heavy gantry crane system on this job proved the ability to install heavy loads Roll Group says. The system can handle loads weighing as much as 3,000 tonnes, lifting to heights exceeding 120 metres. A distinguishing feature of this system is that it can operate without needing guy lines, thereby minimising disruption to the surrounding area, increasing efficiency and occupying minimal space.
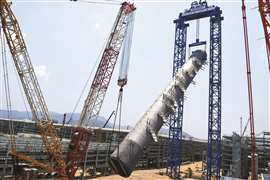
Further scope
In addition to the gantry lifts, Roll Group’s scope included discharging vessels, transporting all cargo and lifting it into position. It meant the company offered the total solution, including engineering, project management, SPMT and five crawler cranes.
The heavy gantry crane system proved itself on these two lifts and two more made in the Middle East, where it will stay for the next two years.
Demand is such for the new gantry system, Roll Group has started fabricating another one, ready to go to work by the end of 2024. This one will boast “enhanced capacity and capabilities, ensuring Roll Group remains at the forefront of the evolving market landscape,” the company says.
Electric options
A new tunnel section was installed using battery-powered jacking and skidding equipment in an emissions-free operation in Belgium.
It started out as a standard skidding operation and turned into a demonstration of how to reduce the carbon footprint of a civils project.
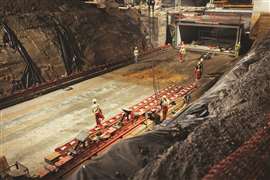
Stadsbader Contractors approached Netherlands-headquartered international heavy lift and transport specialist Mammoet to lift and skid an 850 tonne concrete tunnel section 40 metres underneath railway lines.
Prior to this job, Mammoet gained experience on smaller emissions-free projects to install transformers.
Mammoet determined that this big job could be done without pollution and its engineers worked to combine conventional skidding technology with new battery-powered equipment.
Accurate calculations and precise implementation were needed to lift and skid the 850 tonne concrete tunnel section. It was 25 x 8.5 metres and had to be moved 40 metres into position below a railway track near Brussels.
Mammoet used its own tunnel adaptors and a skidding system with a battery-electric hydraulic power pack. Prior to skidding the load was lifted using hydraulic jacks. When there was enough ground clearance, hydraulic cylinders pushed the tunnel section along the 40 metre skid tracks with their polytetrafluoroethylene (PTFE) pads to minimise friction.
With everything ready the skidding operation took less than an hour and it came out 2.5 hours ahead of the estimated schedule.
Additional benefits of the electric system on the project included lower noise and there was less impact on the surrounding environment because there were no exhaust emissions on site. Time was not an issue either as the operation took no longer than using conventional equipment.
New moves
Lifting and specialized transport contractor Schmidbauer has added new equipment to its fleet for a contract that will see it handle 50,000 tonnes of electrical power cable.
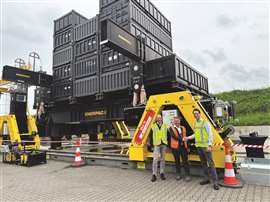
The company bought a 600 tonne capacity Enerpac SBL600 telescopic hydraulic lifting gantry to use on a German power transmission infrastructure project. The SuedOstLink will be a primary power line transmitting green electricity generated in North-East Germany to Bavaria in the south.
Over the next four years Schmidbauer will co-ordinate the handling and storage of 520 cable drums. Each one weighs 95 tonnes. The SBL600 will be set up at several sites to lift the drums from road trailers, hold them and then lower them on to self propelled modular transporter (SPMT) for onward delivery to the point of use off road.
Sideways precision
The gantry’s side shift will help speed up the positioning and accurate placement of the cable drums.
This SBL is Schmidbauer’s first hydraulic telescopic gantry system. Commenting on the move Philipp Verges, sales manager for global projects at Schmidbauer Group, says, “The SBL600 is ideal for the cable reel handling project, and we were especially attracted by the ease of deploying the gantry to site. We’ve invested in six, hard top, standard 20 metre containers which will allow us to easily transport the SBL600 by road, rail and sea to projects worldwide.”
Enerpac’s SBL600 lifts 612 tonnes and offers a 10.6 metre maximum lifting height. The electric side shift is controlled via the wireless system. It means the headroom requirement can be kept to a minimum above the header beam to maximise available lifting height wherever possible.
The vertical lifting leg of the gantry tower can be folded down to save money by allowing transport on standard flat bed trailers.
System tests
Enerpac also recently completed the factory acceptance testing (FAT) on a new system for German customer Lastro Heavylift.
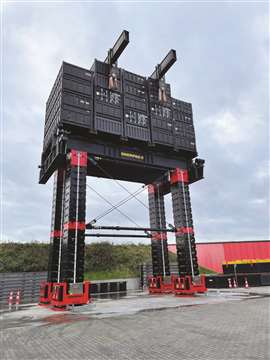
The JS-250 hydraulic jack up lifting system was tested at the factory in Hengelo, the Netherlands by lifting a 660 tonne load to a height of 15 metres. Capacity of the JS-250, configured with four lifting towers, is 1,400 tonnes to a lifting height of 5 metres and 1,000 tonnes to a height of 10 metres.
The new system for Lastro has a bracing kit to triangulate the structure and help resist side loading. It includes four specially designed mid barrels, four adjustable braces and eight diagonal tension bars. The mid barrels are added to the tower and the braces and tension bars are fitted at ground level. As more barrels are added the bracing then rises synchronously, moving to a higher point as the system is jacked up.
Side loading can be expected when using the JS-250 mounted on self-propelled modular transporter (SPMT) in bridge construction applications.
In addition to the JS-250, Lastro has also added 200 tonne and 70 tonne capacity Enerpac strand jacks and an SCJ-Series 100 cube lifting system.
Heavy solutions
Enerpac gantries are proving popular in other parts of the world too. USA-based Engineered Rigging recently expanded its heavy lifting equipment rental fleet with an additional SBL500 hydraulic gantry system.
The SBL500 facilitates infrastructure projects at ports, railways, power and industrial plants – basically any civil or commercial construction application where traditional cranes will not fit and overhead cranes are not an option, the company says.
Christopher Cox, founder and president at Engineered Rigging says, “We expect bidding on large infrastructure projects to increase in 2024, and we stand ready to assist customers with equipment rentals.”
CONECTAR-SE COM A EQUIPE
