SafwayAtlantic beats ground-load limits for access to replace 52-story office
15 December 2022
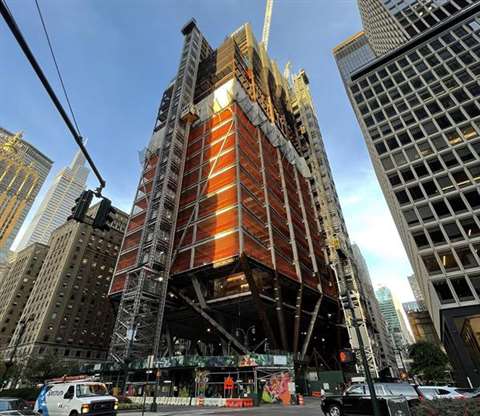
AECOM Tishman chose SafwayAtlantic, by BrandSafway, to create an eight-car personnel and material hoist complex for the 1,388-foot, 60-story JPMorgan Chase global headquarters at 270 Park Ave., New York. The common tower and hoist complex masts will have a total weight and impact load of 6,500 kips (6,500,000 pounds) and hang from pinned connections pushed through steel plates welded to building columns on two floors. No ground loading was permitted due to Metro North train tracks running below ground level.
Previously, AECOM Tishman selected SafwayAtlantic to provide services for the demolition of the old 52-story, 700-foot JPMorgan Chase headquarters, located at the same address. Demolition and new construction started in 2020, proceeding simultaneously, and both had to comply with ground-loading limitations and other challenges.
“Virtually every step required out-of-the-box thinking,” says Tanya Charlesworth, professional engineer and director of engineering for SafwayAtlantic. “AECOM Tishman trusted us with creating first-of-a-kind engineering approaches, and the value to both our businesses is immeasurable. Even in congested urban environments and with extremely tall buildings, we can devise solutions that enable demolition and construction teams to work safely and efficiently.”
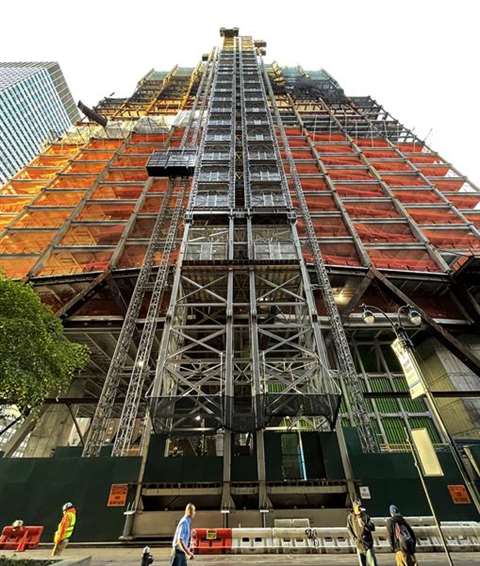
“We custom- fabricated numerous solutions, including a four-car hoist for the demolition, shoring, ground protection, overhead protection, needle beam platforms to support three levels of scaffold during demolition, scaffold ties, edge protection, a debris shoot, the eight-car hanging hoist complex and the world’s longest hoist car,” says Keith Lynch, president of SafwayAtlantic.
Shoring and debris removal
The old and new JPMorgan Chase headquarters occupy the full city block between Park and Madison Avenues and 47th and 48th Streets. Metro North tunnels run underneath three sides of the building (only the building’s Madison Ave. side sits wholly on bedrock). The tunnels were completed in 1875 and some of the structural steel elements have thinned and delaminated. As a result, no loading is allowed on the street above the tunnels. Even then, the tunnels required shoring to withstand the increased construction traffic. SafwayAtlantic engineered and custom fabricated shoring, some of it using high-strength steel to meet a capacity requirement of 130 kips (130,000 pounds).
SafwayAtlantic also fabricated two ground protection platforms rated for 600 pounds per square foot and a 20 kip (20,000 pounds) point load to support the trucks and debris bins that removed a total of 81,600 tons of debris. The platforms tied into the old building’s steel columns (to eliminate ground loading), and a ramp enabled trucks and debris bins to roll on and off the platform.
Innovative solutions facilitate demolition
To demolish the 700-foot-tall tower of the old headquarters, SafwayAtlantic erected Systems Scaffold around its 500-foot perimeter. Because scaffold legs cannot support the weight of 700 feet of scaffolding, SafwayAtlantic installed needle beams on the 41st, 29th and 16th floors to create a cantilevered scaffold platform with a load rating of 300 pounds per square foot.
A steel debris shoot was fabricated and installed in an old elevator shaft. Instead of the traditional cable and orange netting on the exterior of the building, the contractor used BrandSafway’s Rapid-EPS edge protection system, a vertical debris-shielding system made from lightweight aluminum panels attached to compression posts. The panels remove and reinstall easily as demolition progresses, which reduces waste compared to plastic netting. For contractor access to all levels of the old tower, SafwayAtlantic installed a four-car hoist.
World’s longest hoist cars
To move the new building’s curtain walls (aluminum-framed, triple-paned glass panels for the building exterior), SafwayAtlantic worked with RAXTAR to design two dual-mast hoist cars that measure 25 feet long by five feet wide by nine-and-a-half-feet high. Able to carry loads of up to 10,000 pounds at up to 300 feet per minute, they are the longest hoist cars in the world. Designed Access’s EZ call system provides call-to-floor buttons. A loading-dock video display shows hoist location at all times, and cloud-based software books hoist times to reduce overall downtime on the job site.
The hoist complex will also use six conventional hoist cars with 7,000 pounds of capacity. A mast climber from Hydro Mobile, another BrandSafway company, is affixed to the outer masts of the common tower and positioned above the hoist cars. Access crews use the mast climber to erect each successive story of the common tower. It improves scheduling efficiency and eliminates interference with construction crews using the hoist cars.
Construction of the hoist complex began in March 2022, and it will remain in place the scheduled completion date of the new headquarters in 2025.
CONECTAR-SE COM A EQUIPE
